ERP-Systeme verwandeln IoT-Daten in optimierte Prozesse ERP-Systeme in IoT-Plattformen aus der Cloud integrieren
21. April 2017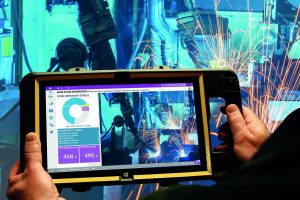
IoT-Daten müssen operationalisiert werden – und das ist die zentrale Aufgabe von ERP-Systemen in Industrie-4.0-Umgebungen. Zum einen steuern sie als Herzstück der Unternehmens-IT die Kernprozesse der Industrieunternehmen und sind damit naturgemäß auch für deren Optimierung durch neue Erkenntnisse zuständig. Zum anderen agieren ihre Anbieter teilweise schon Jahrzehnte am Markt und verfügen deshalb über ein umfassendes Know-how dafür, welche Daten ein Unternehmen genau benötigt, um durch optimierte Geschäftsprozesse für effizientere Abläufe oder höhere Qualität zu sorgen.
Ausgangspunkt Sensordaten
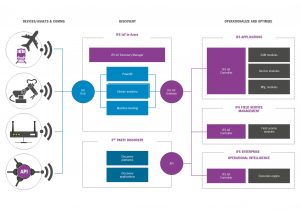
Das Internet of Things (IoT) kann Industrieunternehmen heute Millionen an Sensordaten liefern, aus deren Analyse sich wertvolle Erkenntnisse gewinnen lassen. Diese Informationen nur zu sammeln und auszuwerten reicht aber nicht aus. Um von diesen Big Data wirklich zu profitieren, müssen die Erkenntnisse auch zu Aktionen führen, die die Geschäftsabläufe verbessern, seien es optimierte Wartungspläne, verbesserte Service-Levels, optimierte Logistik, bessere Produkte oder die Entwicklung neuer Geschäftsmodelle.
Die IoT-Daten müssen also operationalisiert werden – und das ist die zentrale Aufgabe von ERP-Systemen in Industrie-4.0-Umgebungen. Ein Beispiel für die Operationalisierung von IoT-Daten im ERP-System sind optimierte Wartungsprozesse. Wenn etwa Sensoren Daten über zu hohe Temperaturen eines bestimmten Teils sammeln, sollten diese nicht nur gesammelt und registriert werden, um dann manuell darauf zu reagieren; das volle Potenzial zeigt sich erst dann, wenn auf Basis dieser Daten ein Prozess angestoßen wird, der automatisch Servicepersonal mit dem Austausch des betroffenen Teils beauftragt und damit seinen Ausfall verhindert. Operationalisieren und Automatisieren – erst durch diese Kombination kann Industrie 4.0 ihre ganze Kraft entfalten und signifikante Umsatzsteigerungen bewirken.
Im ERP-System werden dazu aber nicht sämtliche Daten benötigt, die Industrie 4.0 generiert. Deshalb muss es in eine IT-Architektur eingebunden werden, die die Erfassung, Speicherung und Filterung der Daten ermöglicht. Eine sehr gute Möglichkeit dazu bietet die Integration in IoT-Plattformen in der Cloud. Mit diesen Plattformen lassen sich die riesigen Datenmengen, die unter anderem von den Sensoren geliefert werden, empfangen, verarbeiten, filtern und und an das ERP-System weiterreichen, ohne dafür selbst ein Rechenzentrum aufbauen zu müssen, das Millionen von Transaktionen stemmen kann. Im Sinne einer ganzheitlichen IT-Landschaft wird mittelfristig auch das ERP-System selbst zunehmend in die Cloud wandern; allerdings wird sich dabei hierzulande vor allem das Private-Cloud-Modell durchsetzen. In Deutschland, aber auch in Österreich und der Schweiz sind die Unternehmen – ganz im Gegensatz etwa zu den USA – sehr zurückhaltend wenn es darum geht, geschäftskritische Daten in die öffentliche Cloud auszulagern.
Schritt für Schritt verbessern
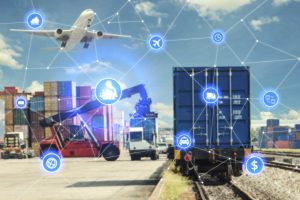
Beim Stichwort Internet of Things kommen vielen Menschen automatisch Unternehmen mit disruptiven Geschäftsmodellen wie der Online-Fahrdienst-Vermittler Uber oder der Video-Streaming-Dienst Netflix in den Sinn, die komplette Branchen auf den Kopf gestellt haben. Industrie 4.0 entwickelt aber in den allermeisten Fällen das vorhandene Geschäft weiter, anstatt es grundlegend zu verändern.
Beim Blick auf Unternehmen, die bereits erfolgreich Industrie-4.0-Anwendungen nutzen, zeigt sich, dass die allermeisten von ihnen mit einem inkrementellen Ansatz gestartet sind. Das kann zunächst auch nur die Anbindung einer einzigen Maschine sein. Erzielt man dadurch ein bisschen mehr Umsatz, kann das die Inspiration für einen größeren Schritt sein – beispielsweise die Integration mit weiteren Daten-Streams wie Wettervorhersagen oder Temperaturänderungen, die es erlauben, die Leistung einer Maschine weiter zu optimieren.
So wird durch zunehmende Vernetzung Schritt für Schritt die Fabrik von morgen entstehen, in der ERP-Lösungen mit Hilfe Künstlicher Intelligenz und Algorithmen sich selbst planende und steuernde Systeme unterstützen. Szenarien wie das Folgende sind dann an der Tagesordnung: Zahlreiche Komponenten in einem Auto sammeln kontinuierlich Daten über ihren Zustand und können auf Basis dieser Informationen mitteilen, wann sie unter Umständen ausgetauscht werden müssen, noch bevor es zu einem möglichen Ausfall kommt.
Dazu sendet die betroffene Komponente selbstständig eine Mitteilung an den Hersteller, dass Ersatz gefertigt werden muss. In der Fabrik, in der dieser Auftrag bearbeitet wird, konfigurieren sich die Maschinen selbst so, dass das passende Teil gefertigt wird und schicken es anschließend an den richtigen Zielort. Der Termin in der Werkstatt ist dann bereits vereinbart – denn auch darum hat sich das Auto bereits selbstständig gekümmert.
Anforderungsprofil
Generell muss ein ERP-System, das sich für Industrie 4.0 eignen soll, die folgenden Funktionalitäten mitbringen:
• Es lässt sich durch Konfiguration statt Modifikation flexibel an die veränderten Rahmenbedingungen anpassen.
• Es kann unterschiedlichste Datentypen verarbeiten, die von Sensoren und Geräten erzeugt werden.
• Zur Kommunikation mit den Ressourcen in der Fertigung kann es über offene Plug-and-Play-Schnittstellen unterschiedliche Produktionsleitsysteme anbinden.
• Leistungsfähige Multi- und Inter-Site-Funktionalitäten sorgen für die Steuerung des erweiterten Informationsflusses über sämtliche, auch internationale Standorte hinweg.
• Zur schnellen Anbindung neuer Partner bietet es offene und leicht konfigurierbare EDI-Schnittstellen sowie spezielle B2B-Portale.
• Um sich selbst organisierende Produktionseinheiten zu ermöglichen, unterstützt es durch Methoden wie Kanban eine hohe Automatisierung.
• Zur Echtzeit-Überwachung von Industrie-4.0-Prozessen führt es Daten und Prozesse aus mehreren Quellen in einem Enterprise-Operational-Intelligence-System zusammen. (rhh)
Stefan Issing und Peter Schulz,
beide IFS Deutschland.