Interoperabilität und Konnektivität: Dreh- und Angelpunkt für Industrie 4.0
19. Juni 2018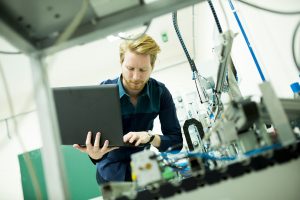
Mit der zunehmenden Vernetzung fürchten viele Mittelständler, in einem Chaos an Daten und Schnittstellen den Überblick zu verlieren. Diese Sorge ist nicht ganz unbegründet: Wer in die Unternehmen schaut, findet statt wohlgeordneter Datenflüsse vielerorts Schnittstellen-Tohuwabohu. Woran liegt das und wie können Unternehmen mit der zunehmenden Vernetzung den Überblick behalten?
Silos haben ausgedient
Vorbei die Zeiten, in denen Anwendungen in sich geschlossene Silos waren. Heute verfügt jede solide Geschäftsanwendung über eine Programmierschnittstelle. Diese Application Programming Interfaces (APIs) bieten eine nie dagewesene Offenheit. Sie ermöglichen, Medienbrüche zu überwinden, vermeiden manuelle Doppeleingaben und damit Fehlerquellen.
Doch diese Offenheit erweist sich als Fluch und Segen zugleich. Denn sie führte und führt zu einer Vielzahl von Eins-zu-Eins-Anbindungen zwischen verschiedensten Applikationen. Würde man versuchen, die Verbindungen aller existierenden Systeme eines Unternehmens aufzuzeichnen, entstünde im Handumdrehen ein unübersichtliches Knäuel von Linien und Pfeilen. Welche Information fließt, unter welchen Bedingungen, wann wohin? Werden die Daten wirklich richtig und vollständig übertragen? Dieser Mangel an Transparenz schürt das Misstrauen der Mitarbeiter in ihre eigenen Daten. Und hinter vorgehaltener Hand gesteht so mancher IT-Verantwortliche, sein Unternehmen habe seine Schnittstellen tatsächlich nicht mehr im Griff.
Die Verbreitung von Industrie 4.0 hebt die Komplexität aktuell auf eine weitere Stufe – und erhöht damit den Druck. Denn das Zeitalter des (Industrial) Internet of Things ermöglicht eine nie dagewesene Vernetzung von Mitarbeitern, Maschinen, Lieferanten und Kunden. Immer mehr Maschinen werden mit Schnittstellen und Sensoren ausgestattet. Digitale Services tauschen Informationen aus und können diese interpretieren. Software kommuniziert mit Hardware, alles ist mit allem vernetzt, auch über Unternehmensgrenzen hinweg. Vor dem geistigen Auge vieler IT-Architekten ziehen dunkle Wolken auf: Sie fürchten ein Schnittstellen-Fiasko.
Standards als Heilsbringer
Das drohende Chaos ruft die Freunde der Regulierung auf den Plan: Standards müssen her, Standards sollen es richten. Unbestritten erleichtern normierte Schnittstellen den Informationsaustausch. Die IT-Geschichte ist voll von positiven Beispielen. Die Debatten, welcher Standard für die Zukunft der richtige sei, haben jedoch eine lähmende Wirkung: Sie verführen die Anwenderunternehmen dazu, auf den universellen Plug-and-Play-Standard für Industrie 4.0 zu warten und das Thema „Smart Factory“ bis dahin „auszusitzen“. Eine gefährliche Strategie, denn diesen Standard wird es in absehbarer Zeit nicht geben. Unternehmen riskieren, international den Anschluss zu verlieren.
Selbst intensive Bemühungen um Branchenstandards werden nicht ausreichen, um die individuellen und aktuellen Anforderungen stets abzudecken. Denn die Bedürfnisse ändern sich laufend. Der aktuelle Standard von heute ist daher immer auch der veraltete Standard von morgen. Außerdem ist Schnittstelle nicht gleich Schnittstelle. Unternehmen brauchen Flexibilität, um ihre Datenströme an ihre Prozesse und die Gegebenheiten des Marktes anzupassen.
Um die Zahl der Schnittstellen zu verringern, ersetzen immer mehr Unternehmen ihr Konglomerat aus Einzelanwendungen durch umfassende Branchen- und Komplettlösungen. ERP-Plattformen wie proALPHA machen mit der Integration eines Dokumentenmanagements, dem Ausbau von Business-Intelligence-Angeboten und durch direkte Kopplung zwischen CAD- und ERP-System so manche Schnittstelle bereits überflüssig.
Weil aber die Markt- und Produktionssituation jedes mittelständischen Unternehmens sehr individuell ist, kann es keine allumfassende „One size fits all“-Lösung geben. Die im deutschsprachigen Raum ansässigen Hidden Champions sind aufgrund ihrer marktführenden Stellung vielfach auch auf hochspezialisierte Anwendungen angewiesen. Diese übernehmen beispielsweise die Steuerung des Shopfloors, das Plant Asset Management, unterstützen die Qualitätssicherung oder übernehmen die Konsolidierung komplexer, internationaler Konzernabschlüsse. Kommen Unternehmen also um eine gewisse Anzahl an Eins-zu-Eins-Verbindungen nicht herum?
Die unternehmerisch effizientere Alternative besteht in der Nutzung einer serviceorientierten Architektur mit einem Enterprise Service Bus (ESB). An eine solche Middleware lassen sich Systeme jeglicher Art relativ einfach andocken. Die gängigen Datenformate XML oder JSON werden ohnehin von vielen Anwendungen bereits unterstützt. Der Bus sorgt für eine stabile und sichere Datenübertragung – ohne Datenverlust.
Gleichzeitig bietet er einen zentralen Verteilmechanismus aller relevanten Daten. Nachrichten können auf unterschiedlichen Wegen (unter anderem via http, ftp, pop3, JMS oder als Datei) auf den Bus gelangen. Nach Bedarf werden die Nachrichten noch transformiert und an das Format des Zielsystems angepasst. Gilt es, mehr als zwei Systeme zu vernetzen, wird schnell klar: Über einen ESB lassen sich Schnittstellen viel einfacher konfigurieren als Eins-zu-Eins-Verbindungen. Um den Aufwand für die Einrichtung eines Bus-Systems zu verringern, integrieren mittelstandsorientierte Anbieter etablierte Middleware in eine konfigurierbare Technologieplattform, wie beispielsweise die Integration Workbench (INWB) von proALPHA. Sie ermöglicht den Unternehmen, ihre Industrie 4.0-Strategie selbst umzusetzen.
Datenkanal gefragt

Wie lohnend dieser Ansatz ist, zeigt die Praxis. Der Anbieter von Parkanlagen KLAUS Multiparking beispielsweise nutzt einen Enterprise Service Bus für den Aufbau einer Predictive-Maintenance-Lösung: „In Zukunft sollen die Nutzungsdauer und -intensität der Parkanlagen permanent überwacht und auf dieser Basis dem Kunden eine vorausschauende Wartung vorgeschlagen werden“, berichtet Geschäftsführer Michael Groneberg.
Die ersten Schritte dazu sind schon getan: „Wir wollen unsere Produkte smarter machen und haben deshalb – zusammen mit proALPHA – einen Prototypen für Predictive Maintenance erstellt, dessen Funktionen künftig in unsere neuen Parkanlagen einfließen“, so Groneberg. In enger Kooperation mit dem Steuerungshersteller, dem Anbieter der Kommunikationssoftware und mit Experten von proALPHA wurde der Prototyp zusammen mit der IT-Abteilung des Mittelständlers aufgebaut. Gemeinsam haben alle Beteiligten innerhalb weniger Monate erreicht, dass die Parkanlage mit dem ERP-System fehlerfrei „sprechen“ kann.
Die IT-Landschaft bei der Günther Spelsberg GmbH + Co. KG war in der Vergangenheit sehr heterogen und wartungsintensiv. Ziel war, externe und interne Systeme problemlos integrieren zu können, um den elektronischen Informationsfluss im Unternehmen zu vereinheitlichen, zu beschleunigen und zuverlässiger zu machen. Mit der INWB ist inzwischen bei Spelsberg die standardisierte Integration sämtlicher externer und interner Systeme möglich – mit der Folge, dass sich viel mehr Nachrichten gleichzeitig austauschen lassen und somit sämtliche Prozesse spürbar schneller sind.
Die Daten aus den jeweils angebundenen Systemen werden quasi in Echtzeit zur Verfügung gestellt. Dadurch kann Spelsberg seinen Kunden aus dem Elektrogroßhandel nun auch eine über das Web zugängliche Informationsplattform anbieten, um Lagerbestände von Standardartikeln einzusehen. Für die Anbindung der Qualitätssicherungssoftware sind jetzt keine eigens programmierten Schnittstellen mehr notwendig. Für den Stammdatenaustausch können Standardreplikationsfunktionen genutzt werden. Ebenfalls ein internes „Fremdsystem“ ist die Maschinendatenerfassung in der Produktion, die nun im nächsten Schritt mit der neuen Datendrehscheibe kommunizieren soll.
Grundlagen für die Digitalisierung sämtlicher Betriebsabläufe, auch international, sind saubere, einheitliche Daten. Bei der Herkules Group beispielsweise werden die Aufträge aus dem Heimatland Deutschland heraus gesteuert. Dennoch müssen auch die zum Verbund gehörenden Firmen in China und den USA auf Zeichnungen, Teilestämme oder Stücklisten zugreifen können – egal, ob sie für eigene Aufträge oder die von anderen Unternehmen der Gruppe fertigen.
Über die INWB lassen sich Daten, Belege oder weitere Informationen schnell und automatisiert austauschen und in die Datenbanken der Standorte China und USA überspielen. So synchronisiert die Gruppe auch ihre derzeit rund 280.000 Teilestämme. Das Werk in den USA wiederum kann beispielsweise die für einen Auftrag benötigten Teile umgehend in Deutschland bestellen. Verzögerungen oder unterschiedliche Informationen über den Konstruktionsfortschritt sind passé.
arüber hinaus lassen sich alle Aktivitäten zwischen den Unternehmen eins zu eins nachvollziehen und konsolidieren.
Dies sind nur einige der unzähligen Integrationsszenarien, die der Einsatz einer serviceorientierten Architektur ermöglicht. Als Bestandteil eines ERP-Systems wird daraus die optimale Steuerungszentrale, die für alle Kommunikationsflüsse im digitalisierten Unternehmen die Weichen stellt.
Johannes B. Imhof
ist Director Research & Development bei proALPHA. Er beschäftigt sich seit Jahren damit, echte Trends von kurzen Hypes im ERP-Umfeld zu unterscheiden und auf dieser Grundlage das Produkt weiterzuentwickeln.
Hier geht es zu proALPHA