Produktion mit kollaborierenden Robotern neu denkenRoboter arbeiten mit Menschen Hand in Hand
25. März 2020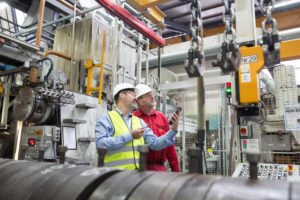
Systeme mit kollaborierenden Robotern, die mit Menschen Hand in Hand arbeiten, sind eine Alternative zu Koexistenz und Kooperation von Mensch und Maschine. Sie können den Menschen entlasten und Tätigkeiten mit immer gleicher Präzision verrichten. Dabei bietet ihr Einsatz eine größere Flexibilität als vollautomatisierte Anlagen und auch eine steigende Qualität, da Stillstände und der dadurch entstehende Ausschuss erheblich verringern lassen. Wer ein kollaborierendes System integrieren will, darf jedoch die Sicherheitsaspekte nicht außer Acht lassen und muss die Produktion ganzheitlich betrachten, um die Roboter optimal einsetzen zu können.
Menschen, die mit Robotern Hand in Hand arbeiten: Die Kollaboration von Mensch und Maschine wird Wirklichkeit, aber noch mit Einschränkungen. Gang und gäbe sind bereits Koexistenz und Kooperation: Wenn Roboter und Mensch zeitlich beziehungsweise örtlich getrennt von Schutzeinrichtungen nebeneinander her arbeiten. Die Kollaboration ermöglicht dagegen die Zusammenarbeit ohne physische oder optische Trennung. Entstehen während der Arbeit Gefahrensituationen geht der Roboter unmittelbar in einen sicheren Zustand über.
Technische Spezifikationen legen die erforderliche Sicherheit fest. Die ISO TS 15066 definiert die Anforderungen für kollaborierende Roboter. Darin beschrieben sind insbesondere die Rahmendaten für die direkte Zusammenarbeit des Menschen mit dem Roboter. Das ist auch der wesentliche Unterschied zur EN ISO 10218, die nur die Koexistenz von Mensch und Maschine abdeckt, nicht aber die Zusammenarbeit.
Wann sind kollaborierende Roboter sinnvoll?
Roboter könnten in der direkten Kollaboration Menschen bei schweren körperlichen oder monotonen Tätigkeiten entlasten, zum Beispiel als Gewichtsentlastung bei der Lastenhandhabung von schweren Bauteilen. Auch in der Operationstechnik sind Roboter sinnvoll, die präzise und kontinuierlich den gleichen Punkt anfahren und genau arbeiten. Schwierige Montagearbeiten können durch ein gemeinsames Arbeiten, etwa, wenn der Roboter dem Menschen die passenden Teile in die Hand gibt, schneller und effizienter erfolgen.
Für den Bau von Getriebesystemen zum Beispiel wäre ein Kollaborationsmodell ideal, da innen verlaufende Zahnräder über spezielle Winkel montiert werden und eine Richtungsänderung während der Montage erfordern. Das geht mit herkömmlich programmierten Verfahrwegen bei Robotern sehr schwer. Viele Unternehmen besitzen sogenannte fahrerlose Transportsysteme für den automatischen Waren-An- und Abtransport. Hier können kollaborierende Roboter, die die passenden Teile aus dem Regal holen und während der Fahrt montieren, eine Unterstützung sein.
Ideal eignen sich kollaborierende Systeme auch für die Medizintechnik, die Leiterplattenindustrie oder die Herstellung von Chips – jene Branchen, für die der Reinraum eine große Rolle spielt und die keine Verunreinigungen während der Produktion tolerieren können.
Vorteile von kollaborierenden Systemen
Je kontinuierlicher eine Fertigungslinie läuft, desto höher ist die Produktausbringung und die Qualität. Das bedeutet, Stillstände müssen unbedingt vermieden werden, da durch das immer wieder neue Anfahren der Linie oft Ausschuss verursacht wird. Diese Stillstände werden oft durch falsche oder nicht ausreichende Sicherheitskonzepte verursacht.
Im Rahmen der Konformitätsbewertung nach Maschinenrichtlinie 2006/42/EG wird zwar innerhalb der Risikobeurteilung die bestimmungsgemäße Verwendung einer Maschine festgelegt, oft wird aber das Produktionsumfeld vernachlässigt. Zur ganzheitlichen Betrachtung gehören alle Lebensphasen der Maschine, also auch die Reinigung, Reparaturen oder die Reaktion auf Umwelteinflüsse und insbesondere die Produktionsbeobachtung zur Fehlererkennung. Gerade bei der Produktionsbeobachtung werden oft vorhandene Schutzeinrichtungen, die ungünstig angebracht sind, umgangen, um Produktionsstillstände zu vermeiden. Das ist einer der häufigsten Gründe für schwere Arbeitsunfälle in der Industrie.
Kollaborierende Systeme können hier einen riesigen Vorteil bieten, da sie den Menschen nicht aussperren, sondern einbeziehen. Das ist möglich, da sie „in sich sicher“ sind. Daraus erwachsen eine größere Flexibilität und mehr Möglichkeiten: Der Mensch kann sich in unmittelbarer Nähe der Maschine aufhalten, sie kann länger laufen, es kommt zu weniger Stillstandzeiten, die geforderte Stückzahl und Verfügbarkeit werden leichter erreicht. Dieser konstante Prozess erhöht die Produktqualität um ein Vielfaches.
Welche Aufgaben können kollaborierende Roboter übernehmen?
Optimal für den Einsatz von kollaborierenden Systemen ist ein Produktionssystem, das sich an der Wertschöpfungskette orientiert und auftragsbezogen produziert. Gerade flexible Produktionen mit zahlreichen Varianten, die direkt auf Kundenbestellungen reagieren, lassen sich mit einem solchen System schneller umsetzen. Über Lesegeräte können Roboter zum Beispiel die richtigen Teile individuell an den Bediener direkt am Laufband reichen – das Band ist flexibel und schneller anpassbar als hochautomatisierte, kostenintensive Anlagen.
Durch die Sensorik können kollaborierende Roboter auch im Qualitätsmanagement zum Einsatz kommen. Durch die Wiederholgenauigkeit können Messfehler durch Ablesen vermieden, bzw. eine größere Stichprobe kontinuierlich gemessen werden. Roboter könnten Menschen so unterstützen und gemeinsam die Qualitätsprüfung verbessern.
Einschränkungen für den Einsatz
Die Kollaboration eignet sich nicht für alle Arten der Produktion. Für zykluszeitkritische Produkte in getakteten Fertigungslinien, Massenware, die innerhalb von wenigen Sekunden hergestellt und verpackt wird, wäre sie zum Beispiel nachteilig: Sie kann die hohen Geschwindigkeiten nicht erreichen, die sich von koexistenten Automatisierungssystemen realisieren lassen. Stattdessen eignet sie sich für hochflexible Fertigungssysteme als Entlastung bei monotonen, bzw. präzisen Arbeiten, die zur schnellen Ermüdung der Muskulatur führen.
Die Hürde liegt in der Sicherheit: Die Roboter dürfen für den Menschen im direkten Kontakt keine Gefahr darstellen. Deshalb bewegen sie sich sehr langsam oder besitzen sensitive Achsen und Gelenke. Findet eine Berührung statt, die über einen gewissen Widerstand hinausgeht, schaltet der Roboter in den sicheren Modus: Die Gelenke werden flexibel und lassen sich wegdrücken, so dass keine Verletzungsgefahr für einen Menschen besteht. Bei einer Bauteilmontage oder einer Verschraubung ist ein gewisser Druck notwendig, daher ist die Gradwanderung zwischen notwendigem Druck ohne Gefährdung eine gewisse Herausforderung für die Programmierung und Umsetzung. Die Kollaboration von Mensch und Maschine ist deswegen nur bedingt serientauglich.
Welche Voraussetzungen müssen bestehen?
Eine Kollaboration von Mensch und Maschine bedeutet nicht einfach, ein neues Prestigeobjekt in seine Produktion zu integrieren. Im Unternehmen muss die Bereitschaft dazu bestehen, sich auf etwas Neues einzulassen und andere Wege zu gehen und auch die Bediener müssen die neuen „Kollegen“ akzeptieren. Kollaboration ist kein Allheilmittel – es muss schon eine genaue Prüfung erfolgen, in welchen Bereichen diese Systeme eingesetzt werden können. Meist gibt das Produkt die Fertigungsart vor.
Der Roboter kann auch nicht einfach autark in die Fertigung gesetzt werden. Stattdessen muss der komplette Materialfluss sicherheitstechnisch durchdacht werden: Neben dem Roboter selbst muss auch die komplette Umgebung auf das kollaborierende System angepasst werden. Wie erfolgt die Materialbereitstellung, wie gestaltet sich die Übergabe zu einer anderen Station, entsteht ein Flaschenhals innerhalb der Produktionskette? Das sind auch Faktoren, die bei getakteten Fertigungslinien einen psychischen Stress bei den Mitarbeitern erzeugen. Der Einsatz muss ganzheitlich gedacht werden.
Sensitive Robotersysteme erfordern, dass die Sicherheitstechnik neu gedacht wird. Sie erfordert ein neues System beispielsweise mit Unterschall-, bewegungssensitiven und optischen Sensoren, die eventuell auch Gestik erkennen können. Bei der Gestik-Steuerung reagiert die Maschine auf bestimmte Signale des Menschen, wie ein Winken oder ein Stoppsignal mit der Hand. Dabei müssen die Sensoren als Sicherheitsbauteile nach Maschinenrichtlinie zertifiziert werden. Ein Experte wie die CE-CON GmbH aus Bremen berät Betreiber von kollaborativen Systemen, welche Anforderungen konkret eingehalten werden müssen und erstellt die Sicherheitskonzepte, um einen sicheren Betrieb gewährleisten zu können. Darüber hinaus unterstützt sie den Hersteller bei der Konformitätsbewertung zur Erlangung der CE-Kennzeichnung.
Warum ist die Robotik heute ein Thema?
Kollaborierende Robotersysteme gibt es bereits seit mehr als 20 Jahren. Doch durch den kontinuierlichen Fortschritt in der Digitalisierung und Informationstechnologie, ergibt sich die Möglichkeit große Datenvolumen einfacher und schneller zu verarbeiten. So sind nun die Voraussetzungen vorhanden, mit optischen Sensoren in Sekundenbruchteilen Bilder aufzunehmen und mit dem Idealzustand abzugleichen. Hier hat die Technologie in den letzten 20 Jahren einen Quantensprung vollzogen.
Die Nachfrage nach kollaborierenden Robotersystemen steigt ständig. Zudem befassen sich immer mehr Unternehmen mit der Thematik. Die mechanische Umsetzung und Weiterentwicklung der Möglichkeiten der Digitalisierung durch den Maschinenbau geht immer schneller. Mittlerweile spricht man innerhalb der globalen Vernetzung von physischen und virtuellen Gegenständen auch vom „Internet of Things“. Dieser Sammelbegriff lässt momentan nur im Ansatz erahnen, was in den nächsten Jahren noch möglich sein wird.
Kollaborierende Systeme können Unternehmen einen konkreten Mehrwert bieten – sie entlasten die Mitarbeiter und bringen für Produktionen mit kleinerer Stückzahl eine große Flexibilität. Um die Systeme sinnvoll einsetzen zu können, ist eine ganzheitliche Betrachtung unbedingt notwendig.
Johannes Spatz, Niederlassungsleiter bei der CE-CON GmbH