Herausforderungen bei der Umsetzung von Industrie 4.0-ProjektenSystemintegration in den Zeiten von Industrie 4.0
13. August 2019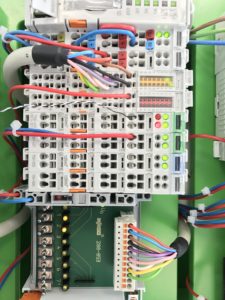
Systeme untereinander verbinden und damit eine Industrie 4.0-Systemintegration aufbauen: Die Umsetzung eines guten Plans sollte nicht an fachlicher oder zeitlicher Überforderung scheitern. Doch das sind unter anderem Gründe, warum Unternehmen mit ihrem Industrie 4.0 Projekt nicht weiterkommen. Datenbanken und verschiedene Quellen zu verbinden und damit die Idee vom Internet of Things (IoT) und Industrie 4.0 anzutreiben, stellt Verantwortliche aber vor eine nur scheinbar schwer lösbare Aufgabe. Eine Middleware kann hier Abhilfe schaffen.
Mehrwert schaffen durch Vergleichbarkeit aller Anlagen: Eine Aufgabe, die verzwickter sein kann, als auf den ersten Blick vermutet. Die Analyse eines Maschinenparks soll die einzelnen Anlagen und ihre Effizienz global vergleichbar machen. Dafür müssen standardisiert Daten erzeugt werden. Eine zentrale Herausforderung im Rahmen von Automatisierung und Industrie 4.0 ist ein in vielen Fällen vorhandenes heterogenes Maschinenumfeld. Doch wer die fünf größten Herausforderungen bewältigen kann, der stellt die Weichen auf Erfolg in seinen Industrie 4.0-Projekten.
Einheitliche Übersetzung aller Protokolle
Oft scheint das Problem unlösbar, alle unterschiedlichen unterstützen Protokolle einheitlich unter einen Hut zu bringen. So sind sie auch einer der häufigsten Gründe, warum Industrie 4.0 Projekte scheitern: Unterschiedliche Maschinenarten und -typen oder gleichartige mit jeweils anderen Baujahren oder Herstellern, die deswegen unterschiedliche Sprachen unterstützen.
Um aus der Ansammlung diverser Systeme mit Sprachen, die scheinbar nicht standardisiert werden können, Mehrwert ziehen zu können, müssen diese Daten überein oder in Verbindung gebracht werden. Eine komplexe Aufgabe: Doch in diesen Fällen gibt es eine leicht umsetzbare Lösung, der Einsatz eines Software-Tools, das alle Protokolle in OPC als Standard-Protokollsprache übersetzt – ein OPC-Server (wie z. B. KEPServerEX).
In Verbindung mit der richtigen Middleware ermöglicht dies die Kommunikation der verschiedenen Systeme und Maschinen – egal welche Sprache diese sprechen. Die plattformunabhängige Möglichkeit zur Kommunikation zwischen verschiedenen Geräten wird in allen Automatisierungsebenen verwendet und ermöglicht die Verbindung zwischen einer Vielzahl von Systemen. OPC UA gilt daher als eines der wichtigsten IoT- / Industrie 4.0-Protokolle. Die Middleware fungiert dann als OPC-Client-Software für OPC DA und OPC UA und garantiert Leistungsfähigkeit für gesicherte Kommunikation.
Individuelle Lösung für Exoten
Ein weiterer Grund, der für Stagnation eines Industrie 4.0 Projektes sorgen und dem Automatisierer oder Instandhalter die Analyse oder Effizienzoptimierung erschweren kann, sind seltene Anlagen, inklusive seltener proprietärer Protokolle, die es gar nicht in standardisierter Form gibt. Dies können spezielle Drucker sein oder auch CNC-Maschinen mit eigenen Protokollen. Um Konnektivität zu schaffen und die Maschinen ins Netz zu bringen, spielt die richtige Middleware auch hier ihre Vorteile aus, da sie über entsprechendes Scripting native Treiber wie für zum Beispiel Anlagen des Herstellers Heidenhain erstellen kann. Vorteil: Die Aufzeichnung von Prozesswerten, Produktionszahlen, Störzeiten und -gründen oder Verbräuchen sind die Grundlage für die Optimierung der Produktion.
- Individuelle Plug-in-Erstellung für diverse Verbindungsarten, Übersetzungen auch für seltene Systeme.
- Mancher Exot wird in verschiedenen Branchen eingesetzt, neue Plug-ins sind mit der nächsten Softwareversion verfügbar.
- Erstellung einzelner Anbindungen und Transfers über grafische Konfiguration.
Operational Technology (OT) mit IT verbinden
In vielen Fällen sorgt auch die Anbindung an kaufmännische Systeme während Industrie 4.0 Projekten für eine Herausforderung, weil zum einen unterschiedliche Sichtweisen der IT- und OT-Welt zu Verständnisproblemen führen und zudem die Umsetzung der Anforderung schnell zu komplex oder teuer wird. Den Brückenschlag zwischen IT und Automatisierung vollzieht eine Middleware, wenn diese mit entsprechenden Plug-ins eine Kopplung an SAP oder andere kaufmännische Systeme ermöglicht.
Daten im OPC-Format aus der Steuerung werden einfach in SAP übertragen. Es entsteht eine Kommunikationsschnittstelle zwischen Produktion und kaufmännischem Bereich. Durch die Verknüpfung von IT und OT wird Zeit, aber auch bares Geld gespart. Die Entwicklung, Dokumentation und Pflege einer individuellen Schnittstellle kann schnell den vielfachen Preis einer standardisierten Middleware-Software betragen.
Anbindung aller beteiligten Systeme
Drucker, Kamerasysteme, Wiegesysteme, Laborsysteme, Barcode-/Handscanner, RFID Reader/Writer: Unternehmen brauchen mehr als einzelne Daten vom Förderband, alle Geräte an der Produktionslinie müssen angebunden werden. Die unterschiedlichen Systeme sprechen nicht nur unterschiedliche Protokolle, sondern sind auch bezüglich der Technologie komplett verschieden. Es ist ein komplexer Prozess, zu überblicken, welche Systeme miteinander kombiniert werden müssen, um Mehrwert zu erhalten.
Aufwand und auch fachliche Überforderung angesichts der Vielzahl an Individuallösungen, die ins Netz gebracht werden müssen, können dazu führen, dass ein Industrie 4.0 Projekt scheitert oder zumindest ins Stocken gerät. Da unterstützt ein Tool, das für alle Sonderlösungen und jedes Kommunikationsprotokoll effektiv eine Anbindung schafft. Eine passende Middleware sammelt alle Daten zu einem Vorgang aus den unterschiedlichen Datenquellen und stellt so die Dokumentation im Rahmen von validierten Prozessen sicher. Unternehmen sparen zudem den Aufwand, jedes Protokoll eigenständig bearbeiten zu müssen.
Relevante Daten zentral zur Verfügung
Häufig können nicht alle relevanten Daten zur Verfügung gestellt werden, sondern werden in ganz unterschiedlichen Systemen vorgehalten, etwa in Steuerungen, Clouds, Datenbanken oder lokalen Computersystemen. Dabei ist eine zentrale Speicherung oft elementar und dafür müssen Daten aus den diversen Quellen geholt und dann gesammelt gespeichert werden – in den Formaten und Protokollen, die von dem jeweiligen Zielsystem benötigt werden, z. B. im OPC-, SQL-. MQTT-, REST- oder JSON-Format. Durch eine passende Middleware müssen Daten nun nicht mehr manuell zusammengetragen werden, somit wird der Worst Case verhindert:
Ein durch und durch digitalisiertes Unternehmen muss bei der Zusammenführung von Daten auf die Papierversion zurück wechseln. Alle relevanten Daten sind gebündelt in der Cloud oder einer Datenbank, um so Zustände und Effizienz der weltweiten Anlagen zu erkennen, an einer beliebigen zentralen Stelle. Im Rahmen von Condition Based Monitoring- oder Predictive Maintenance Systemen kann so rechtzeitig eingegriffen werden, schon bevor eine Anlage stillsteht. Eventuelle Probleme können durch direkte Vergleichbarkeit aller relevanten Daten leicht analysiert und schnell beseitigt werden.
Fazit
Damit die Vernetzung und Interaktion aller Beteiligten in der industriellen Produktion gelingt, greifen immer mehr Unternehmen auf ein Tool als Middleware und zentrale Kommunikationsplattform zurück, das automatisierten Datenaustausch durch komplette Integration aller Systeme und Insellösungen wie etwa OPC UA, SAP und SQL bietet. Als eine umfassende Lösung dient zum Beispiel der OPC Router als Datenlogger, Machine to Machine-Gateway, IoT-Treiber und Schnittstelle zwischen speicherprogrammierbarer Steuerung und anderen Systemen wie ERP, Datenbank oder E-Mail und optimiert somit die bisherigen Kommunikationswege.
Daniel Knep, IT-Journalist, Thorsten Weiler, Leiter Vertrieb Inray und Jonas Schramm, Projektentwicklung Inray