Security zwischen Risikomanagement und Wertschöpfung Hightech-Manufacturing braucht Sicherheit
13. Juli 2017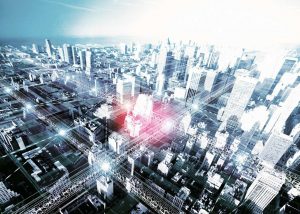
Wer künftig am Wertschöpfungspotenzial von Smart-Industry-Lösungen partizipieren möchte, muss in punkto Sicherheit umdenken. Denn mit zunehmender Komplexität des Lieferketten-Ökosystems steigen auch die potenziellen Risiken. Cybersecurity ist damit längst kein Selbstzweck mehr, sondern eine der entscheidenden unternehmerischen Voraussetzungen für den Erhalt der Wettbewerbsfähigkeit in Zeiten der digitalen Transformation. Doch gewachsene Strukturen erweisen sich oftmals als Sicherheitsproblem.
Wachstumsprognosen
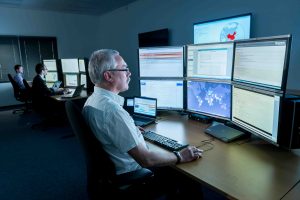
Wenn es um die Digitalisierung der Wirtschaft geht, überschlagen sich inzwischen die Wachstumsprognosen. Folgt man führenden Wirtschaftsexperten, so warten auf die deutsche Industrie brachliegende Wertschöpfungspotenziale im dreistelligen Milliardenbereich. Eine 2014 durchgeführte Studie des BITKOM-Verbandes schätzt etwa, dass sich durch Industrie 4.0 allein in den Fertigungsbereichen Automotive, Maschinenbau und Elektronik bis zum Jahr 2025 eine zusätzliche Wertschöpfung in Höhe von rund 50 Milliarden Euro ergeben könnte.
Handlungsbedarf ist indessen noch nicht in allen Wirtschaftsbereichen in gleichem Maße gegeben. Die Industrie, im speziellen die Hightech-Fertigung, sieht sich bereits heute einem enormen Digitalisierungszwang ausgesetzt. Denn immer kürzer werdende Produktlebenszyklen und steigender Wettbewerbsdruck machen die digitale Fabrik schon allein aufgrund ihres hohen Optimierungspotenzials für die immer komplexer werdenden Lieferketten zu einem der entscheidenden Zukunftsfaktoren.
Zumal der Produktionsprozess eines Flugzeugs, Automobils oder die Herstellung eines Smartphones heute nicht mehr aus einer einzelnen Lieferkette besteht, sondern vielmehr die Summe aus hunderten von verzahnten, exakt aufeinander abgestimmten Wertschöpfungsprozessen und Fertigungsschritten darstellt. Unter diesen Vorzeichen auf Industrie 4.0 zu verzichten, hieße, hart erarbeitete Technologievorsprünge preiszugeben und damit langsam aber sicher seine Marktrelevanz zu verlieren.
Auch wenn jeder Technologiehersteller im Rahmen der digitalen Transformation seine ganz eigenen Strategien entwickeln und umsetzen muss, so teilen alle Smart-Industry-Konzepte letztlich ein gemeinsames Paradigma: Die Fertigung der Zukunft ist datengetrieben, vernetzt und transparent. Produktionsprozess, Materialfluss und ERP-Informationen verschmelzen, gleichzeitig wächst die Anzahl von Echtzeitdatenströmen und Verbindungen exponentiell an – und damit auch die Zahl möglicher Sicherheitslücken. Schon jetzt zeigt sich, dass „klassische“ Sicherheitskonzepte, die hauptsächlich auf einer Trennung von Produktionssystemen und Office-IT beruhen, den Herausforderungen der digitalen Fabrik nicht mehr standhalten werden.
Eine Strategie des digitalen Wandels muss deshalb auch die Voraussetzungen für den sicheren Betrieb neuer Technologien einschließen, bei denen die Grenzen zwischen IT-Ebene und Produktionssystemen zunehmend verschwinden. Die technologische Neuausrichtung bietet hierbei einen perfekten Einstiegspunkt für eine grundlegende sicherheitstechnische Bestandsaufnahme und die Bewertung möglicher Sicherheitsrisiken, gerade im Hinblick auf die Planung der eigenen digitalen Agenda.
Auch wenn die industrielle Digitalisierung oftmals als Revolution dargestellt wird, so gleicht sie im Prinzip einem kontinuierlichen Prozess, der bereits in den achtziger und neunziger Jahren begonnen hat. Als die moderne Automatisierungstechnik ihren Anfang nahm, steckte das Internet noch in den Kinderschuhen. Niemand hat seinerzeit ernsthaft an die Möglichkeit gedacht, Produktionssysteme mit dem Internet zu verbinden. Industriesteuersysteme wurden als isolierte Einheit betrachtet – Sicherheitsfunktionen wie Authentifizierungsmechanismen, Passwortmanagement oder Zugriffsbeschränkungen waren demnach nicht notwendig und auf Protokollebene schlichtweg nicht vorgesehen. Für ein Produktions-Subsystem genügte es, per Zweidrahtleitung oder Funk an eine höhere Hierarchie wie beispielsweise ein SPS-System angeschlossen zu sein, denn praktische Vorteile wie Echtzeitfähigkeit und Zuverlässigkeit waren die entscheidenden Parameter im Produktionsverbund.
Doch trotz der hohen Echtzeitanforderungen ist das Zeitalter des Internets nicht spurlos an der Fertigungsebene vorbeigezogen. Wo die Flexibilität von TCP/IP von Nutzen war oder Kosten eingespart werden konnten, wurden in den vergangenen Jahren viele Verbindungen auf das IP-Protokoll umgestellt – jedoch nicht immer mit der notwendigen Systematik und nur selten mit dem entsprechenden IT-Sicherheitsbewusstsein.
Einer der Haupttreiber war dabei die Bereitstellung von Fernzugängen. Technikern und Wartungspersonal von Anlagenherstellern sollte ein schneller Zugriff auf die Managementoberflächen von Produktionssystemen ermöglicht werden, um Konfigurationsänderungen vorzunehmen, den Status von Maschinen einzusehen oder wichtige Updates einzuspielen – und dies, ohne dabei hohe Arbeits- oder Anreisekosten zu verursachen. Als Folge entstanden so organisch gewachsene Vernetzungsstrukturen mit einer heterogenen Architektur aus industriespezifischen Protokollen, lokalen Netzknoten mit Anbindung an die Office-IT und mehr oder weniger offenen Internet-Zugängen – meist mäßig dokumentiert, unzureichend segmentiert und mangels verfügbarer Richtlinien auch ohne einheitliche Standards für Zugriffsmanagement und Passwortsicherheit.
Fachübergreifenden Konsens
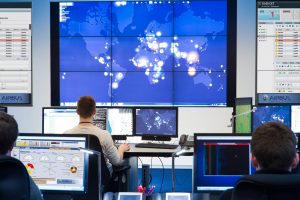
Bei Produktionsspezialisten und Automatisierern mag der Mix-and-Match-Zustand vieler Industrienetze zunächst keine Bedenken auslösen. Denn immerhin werden Funktionen, die die Betriebssicherheit von Anlagen gefährden könnten, auf Feldebene getrennt ausgeführt und redundant ausgelegt. Sicherheitsrelevante Grenzwerte wie Maximaldrücke oder Drehzahlen von Pumpen sind ohnehin hartkodiert. Hinzu kommt, dass die verwendeten industriespezifischen Protokolle für mögliche Angreifer eine hohe technische Hürde darstellen.
Angesichts der Entwicklung der vergangenen Jahre reichen diese Aspekte für sich allein jedoch nicht mehr aus. Denn nicht nur die Anzahl der IP-Verbindungen hat bereits stark zugenommen, sondern auch die Bedrohungslage selbst ist heute eine völlig andere als vielleicht noch vor fünf Jahren. Spätestens seit dem Auftauchen von Stuxnet sowie weiteren, auf Industrienetze spezialisierten Malware-Varianten wird die Diskussion über Sicherheit in Produktionssystemen verstärkt in der Öffentlichkeit geführt.
Hinzu kommt, dass inzwischen auch spezialisierte Suchmaschinen existieren, die gezielt nach offenen Internetverbindungen mit produktionsspezifischen Protokollen suchen können. Eine aktuelle ICS-Security-Studie des Sicherheitsspezialisten Kaspersky Lab lieferte unlängst rund 26 000 unsichere ICS-Komponenten, die allein in Deutschland problemlos über das Internet erreichbar waren. Das dies kein wünschenswerter Ist-Zustand für den reibungslosen Betrieb einer Produktionsumgebung sein kann, ist mittlerweile fachübergreifender Konsens.
Auch das ursprüngliche Silo-Denken zwischen IT-Verantwortlichen und Produktionsleitern löst sich dank zunehmender Berichterstattung, vermehrter Aufklärung in Forschung und Lehre sowie standardisierter Sicherheitsrichtlinien (IEC 62443) mehr und mehr auf. Inzwischen werden professionell koordinierte Sicherheitsinitiativen von den meisten Produktionsleitern begrüßt oder sogar aktiv gefordert. Immerhin sind sie letztlich für einen reibungslosen Fertigungsablauf und einen effizienten Anlagen-Output verantwortlich.
Ein komplexer Hackerangriff oder ein auf Industrieanlagen spezialisierter Schädling gefährdet diese Zielsetzung. Laut dem BSI vergehen 227 Tage, bis eine gezielte Attacke auf ein Unternehmen bemerkt wird – so lange sitzt der Angreifer im Durchschnitt im Unternehmen, kann spionieren, Manipulationen vorbereiten, ohne dass jemand weiß, dass ein Problem vorliegt. Schon ein einzelner Sicherheitsvorfall kann zu langanhaltenden und sehr teuren Produktionsausfällen oder zur Offenlegung brisanter Betriebsgeheimnisse führen – speziell in der Hochtechnologiefertigung wie auch beim Aufbau der Produktionsumgebung selbst, denn in der Architektur von Feldbusebene und MES-Systemen sowie der Parametrisierung von speicherprogrammierbaren Steuerungen steckt mitunter jahrzehntelanges Entwicklungs-Know-how und damit geistiges Eigentum, das unbedingt geschützt werden muss.
Bis zu 51 Milliarden Euro Schaden in Unternehmen werden pro Jahr, so eine Studie der Bitkom, aufgrund von Cyber-Attacken verursacht. ICS-Security wird deshalb schon längst nicht mehr als Hemmnis für die Fertigung gesehen, sondern vielmehr als eine der entscheidenden Voraussetzungen für eine zuverlässige Produktionsplanung. Dieses Umdenken war zwingend nötig, denn ohne die Fachkenntnis von Produktionstechnikern und Prozessleitingenieuren lassen sich Fertigungsumgebungen nicht praxisgerecht absichern.
Erst ein interdisziplinärer Ansatz, bei dem die Sichtweisen von IT- und Produktionsspezialisten sinnvoll zusammengeführt werden, ist in der Lage, Echtzeitanforderungen und Sicherheitsmechanismen zu einem ausbalancierten Sicherheitskonzept zu verbinden. Dabei müssen auch IT-Security-Spezialisten ihre Sichtweisen überprüfen und gegebenenfalls einen nachhaltigen Perspektivwechsel vornehmen, denn auch ein übertriebener Einsatz von IT-Security-Maßnahmen ist in der Feldebene nicht zielführend. Er würde letztlich in einen starren Produktionsverbund münden, der an den Praxisanforderungen der Fertigungsumgebung vorbeigeht. Deshalb gilt gerade bei der Absicherung von Fertigungsumgebungen: “One-size-fits-all“-Lösungen sind meist fehl am Platze, entscheidend sind die individuellen Anforderungen des einzelnen Betreibers.
Risikobewertung
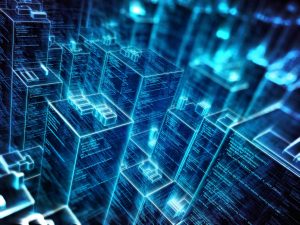
Für einen Security-Anbieter liegt die Herausforderung bei der Absicherung von Produktionsumgebungen deshalb vor allem darin, maßgeschneiderte Sicherheitskonzepte zu finden, die sich technisch und organisatorisch nahtlos in die vorhandenen Fertigungsabläufe einbetten lassen. Voraussetzung hierfür sind nicht nur theoretische Grundlagenkenntnisse und ein gut ausgebildetes Spezialisten-Team, sondern auch ein hohes Maß an Praxiserfahrung. Als eines der führenden Hochtechnologieunternehmen Europas blickt Airbus auf eine lange Tradition in der Fertigung von Hightech-Produkten mit hohem Schutzbedarf zurück. Viele Erfahrungswerte und analytische Methoden des Geschäftsbereichs Cyber Security stammen dabei direkt aus dem unternehmenseigenen operativen ICS-Umfeld und haben sich in der Praxis schon vielfach bewährt.
Industrial Security ist, wie auch der digitale Wandel insgesamt, kein definierter Endzustand, sondern ein kontinuierlicher Prozess. Ein grundlegender erster Schritt auf dem Weg zu einer validen ICS-Sicherheitsstrategie muss deshalb eine detaillierte Risikoanalyse sein. Diese Vorgehensweise empfiehlt auch das Bundesamt für Sicherheit in der Informationstechnik (BSI). Im ICS-Security-Kompendium des BSI heißt es hierzu:
„Die Durchführung einer wiederkehrenden (regelmäßigen bzw. anlassbezogenen) Risikoanalyse wird als verpflichtend angesehen“. Im Rahmen seiner umfassenden Security-Services entwickelt Airbus Cyber Security ganzheitliche Sicherheitsstrategien, die exakt auf solch einer Analyse basieren. Zielsetzung ist dabei, in direkter Zusammenarbeit mit IT- und Produktions-Teams des Betreibers die fünf Top-Risiken zu identifizieren und zu dokumentieren sowie praktikable Gegenmaßnahmen zu empfehlen. Die Zielsetzungen umfassen im Einzelnen:
• Den Aufbau von sicheren Remote-Zugängen für Wartung und Analyse,
• die Absicherung des Produktionsverbundes sowie die Isolierung oder Überwachung von mit Schwachstellen behafteten Altsystemen durch passive Security Sensoren,
• die Sicherung von Endpoints, Datenbanken und Servern (MES, HMI-Stationen, Notebooks und Mobilgeräten),
• die sichere Nutzung von portablen Medien wie USB-Sticks oder CDs sowie
• den Wissenstransfer und die Bereitstellung einer Methodik für eine kontinuierliche Risikoanalyse.
Die Absicherung von Produktionsanlagen ist gerade für Hochtechnologieunternehmen eine komplexe Herausforderung mit zuweilen hohem Kostenaufwand. Vor dem Hintergrund von Industrie 4.0 und IoT (Internet of Things) ist eine sicherheitstechnische Bestandsaufnahme jedoch unumgänglich, um den digitalen Wandel auf eine solide Basis zu stellen.
Ein Security-Assessment bietet dazu einen sinnvollen Einstiegspunkt und ist der Grundstein für alle weiteren Handlungsempfehlungen sowie den Aufbau einer langfristigen Sicherheitsstrategie. Die Kosten der Analyse bleiben dabei in einem überschaubaren Rahmen und amortisieren sich schnell durch die Minimierung von Ausfallrisiken sowie einen insgesamt zuverlässigeren Produktionsverbund. (rhh)
Hier geht es zu Airbus Cybersecurity