Software-gestützte Fertigungsplanung mittels APS
19. Juli 2017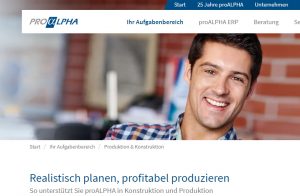
Wer es sich heute noch leisten kann, chronologisch einen Produktionsauftrag nach dem anderen abzuarbeiten, braucht kein Advanced Planning und Scheduling. Für alle anderen Fertigungsunternehmen ist eine Software-gestützte Produktionsplanung erfolgsentscheidend – denn Aufträge und die dafür nötigen Ressourcen müssen abgestimmt auf die Unternehmensziele orchestriert werden.
Optimieren nach individuellen Zielen: Ältere Produktionsplanungs- und Steuerungssystems (PPS) orientieren sich dabei oft nur an der kostengünstigsten Losgröße. Aber zusätzlich zu Kostenaspekten müssen sich Fertiger heute auch nach anderen betriebswirtschaftlichen Faktoren ausrichten, etwa nach Durchlaufzeiten oder Liefertermintreue. Das APS muss sich also flexibel individuellen Zielen anpassen – und dabei auch mehrere Fertigungsarten parallel unterstützen, vom Einzelauftrag über Variantenfertigung bis zur Großserie.
Standortübergreifende Planung: Ein APS erstellt nicht nur einen realistischen Gesamtplan, es aktualisiert sich auch laufend entsprechend der aktuellen Auftrags-, Lieferanten- und Ressourcen-Situation. Dabei muss es mehrere Produktions- und Auslieferstandorte mit einbeziehen können. Bei MAJA-Maschinenfabrik aus dem Ortenaukreis beispielsweise ordnet das APS-Modul des ERP-Systems proALPHA die zu fertigenden Teile den verschiedenen Standorten zu und legt die notwendigen Kapazitäten fest – etwa von Arbeitskräften und Betriebsmitteln.
Mehr als Mitarbeiter, Maschinen und Werkzeuge: Eine effiziente Multiressourcenplanung synchronisiert nicht nur Mitarbeiter, Maschinen und Werkzeuge. Sie berücksichtigt sämtliche relevanten Faktoren. Im Fall von MAJA fließen unter anderem Nachfrage, Distribution und Transport in die APS-Berechnungen mit ein. „Das System bringt damit wesentlich mehr Transparenz und Flexibilität in unsere betrieblichen Prozesse“, sagt Bernd Schäfer, Leiter Personal & EDV bei MAJA.
Planungsgenauigkeit, auf den Punkt: Mit APS gelingt es, bisher nötige Puffer in der Materialbereitstellung abschmelzen zu lassen. Überkapazitäten im Materialbestand oder Übergangszeiten in der Materialbereitstellung werden minimiert. Gleichzeitig muss die APS-Software Puffer so bemessen, dass keine Engpässe entstehen. Und sie muss so genau kalkulieren, dass ad-hoc haltbare Capable-to-Promise-Aussagen möglich sind.
Parallelisieren soweit sinnvoll und machbar: Durchlaufzeiten lassen sich signifikant verkürzen, wenn Arbeitsgänge parallel abgearbeitet werden und sich Teillose überlappen. Auch das parallele Bearbeiten mehrerer Aufträge in einem Arbeitsgang, etwa beim Galvanisieren oder Lackieren, sollte ein APS-System berücksichtigen. Dann werden Ressourcen besser ausgelastet, weniger Aufträge gehen an die verlängerte Werkbank. „Die Verbesserungen in den Prozessabläufen, die Zufriedenheit unserer Mitarbeiter sowie der daraus entstandene Gewinn an zeitlichen und auch finanziellen Ressourcen spricht für sich“, bestätigt Silke Ridener, IT-Leiterin bei Walther-Werke Ferdinand Walther GmbH, die Vorteile von APS.
Einfaches manuelles Eingreifen: Trotz aller Automatisierung muss manuelles Eingreifen immer möglich sein. Selbst wenn, wie bei MAJA, drei- bis viermal am Tag die Planung neu berechnet wird: Denn eine defekte Maschine oder ein erkrankter Mitarbeiter, der nach Hause geht, ist einfach nicht vorhersehbar. Dann muss sich die Feinplanung per Drag-and-Drop rasch anpassen lassen.
Echtzeitdaten und „Single Source of Truth“: Ein APS-System muss heute Daten in Echtzeit verarbeiten können: In Zeiten von Industrie 4.0 ist das kein Luxus mehr, sondern eine Notwendigkeit. Zusätzlich sollten Unternehmen auf einen reibungslosen Informationsfluss zwischen Produktionsplanung, Materialwirtschaft und Konstruktion achten. So lässt sich mit Hilfe von APS die Effizienz noch weiter erhöhen. (rhh)
Hier geht es zu proALPHA